The Hand Engraving Process
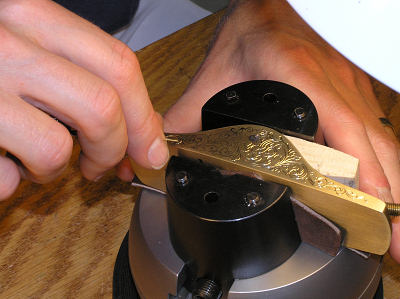
Hand engraving has been used to embellish fine metal work for centuries. It is accomplished by carving precise grooves in the surface with a graver, which is essentially a tiny chisel. The graver can be pushed through the metal by hand or driven with a small hammer, depending on the size of cut required. Recently, pneumatically-driven handpieces have been developed, which combine the power of the hammer with the finesse of the hand-pushed graver. The essential process remains the same even with modern tooling; the design must be well thought out, and the cutting must be skillfully executed with smooth, flowing lines for a beautiful result.
Valdemar Skov designs monograms based on classic letterforms, combining letters and often incorporating flourishes as appropriate, to create a balanced, pleasing design. The monograms vary in layout as each letter combination offers different possibilities, and the individual letters (excluding flourishes) generally range from about one-quarter to one-half of an inch high, depending on the space available and letter style. Monograms or other inscriptions can be combined with ornamental designs. Ornamental engraving can take forms ranging from simple calligraphic swirls to richly detailed intertwining spiral scrolls and leaves flowing across the surface. Like high quality lettering, good scrollwork requires careful planning and execution to appear graceful and balanced.

During the cutting process, Valdemar uses an air-powered handpiece with gravers having various cutting profiles. The tool is held in the palm of the right hand, much as you might hold a small screwdriver, and the sharpened tip is pushed along the metal surface to cut a (very) small groove. For straight cuts, the tool is pushed across the work, from right to left; curved cuts are made by holding the tool steady and turning the work into the tool. The work is held in an engraver's block or some other fixture that allows it to be rotated freely as it is cut. This allows very precise control of the tool's cutting angle, which affects the width, depth and smoothness of the cut. The quality of the engraving is directly related to the degree of tool control exercised by the engraver.
Hand engraving should not be confused with machine engraving, which scratches the metal surface with a rotary diamond burr, following a template or computer generated pattern. This leaves a shallow groove with a rough surface. Hand engraving is cut freehand, so that the artist has complete freedom in design, and the smooth, deeper cuts from hand engraving will not wear away even after years of use. A machine also cannot duplicate the sparkle, or the variation in width and depth of cut that gives life to a hand engraved design; from the bold spirals that form the backbone of a design to the finest shading cuts.
